I recently worked as an Electrical Engineer for Navmar Applied Sciences Corporation. In 2016, the Navy asked me to return to their programs in a non-deployment role to assist with their testing efforts at Yuma Proving Ground. Shortly after rejoining many of my old comrades, the Navy began transferring the surveillance balloon and tower operations to the Army. At that time, an opportunity arose for me to join the Tigershark unmanned aircraft program and I accepted the position. I started at the bottom and worked my way up over the course of 18 months. I began training as a UAS (Unmanned Aircraft Systems) technician. After I mastered all aspects of assembly, maintenance, and repair of the aircraft, I added flight line operations, and eventually, full Mission Commander duties. We operate and maintain a fleet of a dozen aircraft for testing experimental military and government payloads.
In January of 2020, I transferred from a flight operations position in Arizona to the engineering team at the NASC headquarters in Pennsylvania where I worked on electronics and electrical designs for future unmanned aircraft.

Dual Tigersharks, carrying small drones under the wings. The Tigershark is a mid-size unmanned aircraft, featuring a 22-foot wingspan.

I am also the logistics site lead for the Tigershark program in the Western United States. I manage over $200 million in inventory for the program, and I handle all shipping and receiving of government property. My first task upon joining the team was to coordinate the movement of over 200 shipping containers from Yuma Proving Ground to Naval Air Field - El Centro.
After completing that move, my next logistics task was to implement an inventory tracking system for our site at Yuma Proving Ground. I created a parts database using Microsoft Visual Basic for Applications and entered the hand-written inventory information for over 5,000 individual parts. The current system enables location tracking, quantities, vendors, alerts to flag re-order, and many other parameters.
While working on the Tigershark program, I continue to keep my CAD skills sharp. When the design for a critical tool was lost, I took apart the last remaining specimen and reverse-engineered it. The organization was able to use my new drawings to have several replacement tools manufactured. This is a rendering I created from my design. The tool is for removing and installing high-pressure compressed gas lines.
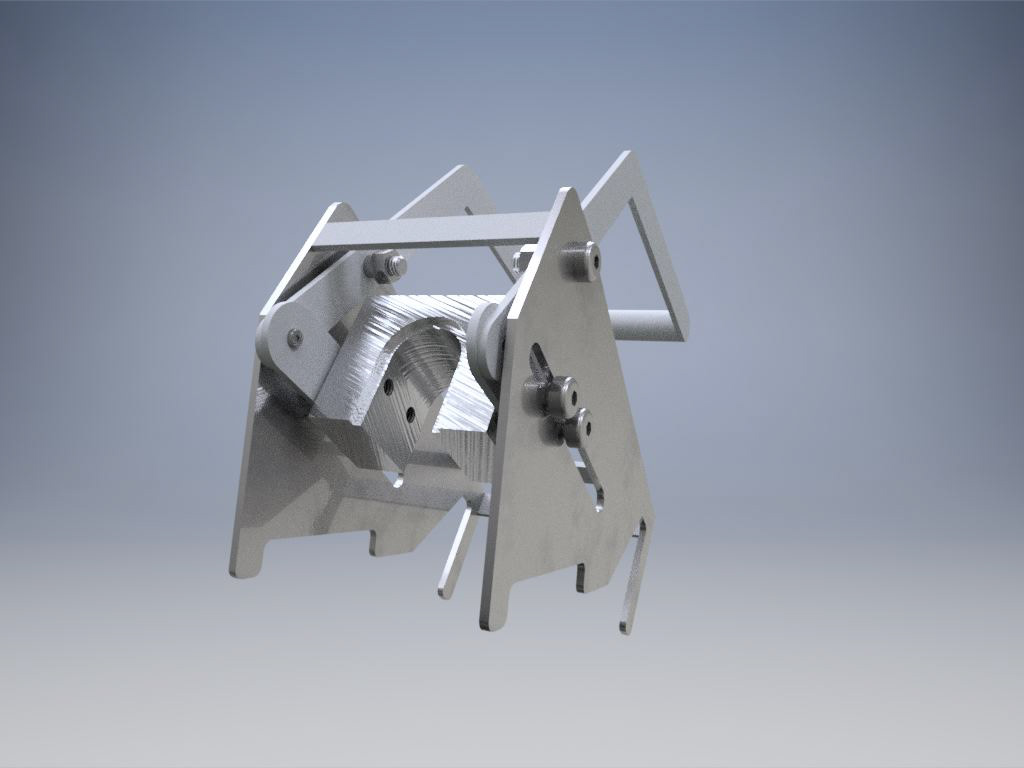
CAD rendering of high-pressure gas line connect/disconnect tool.
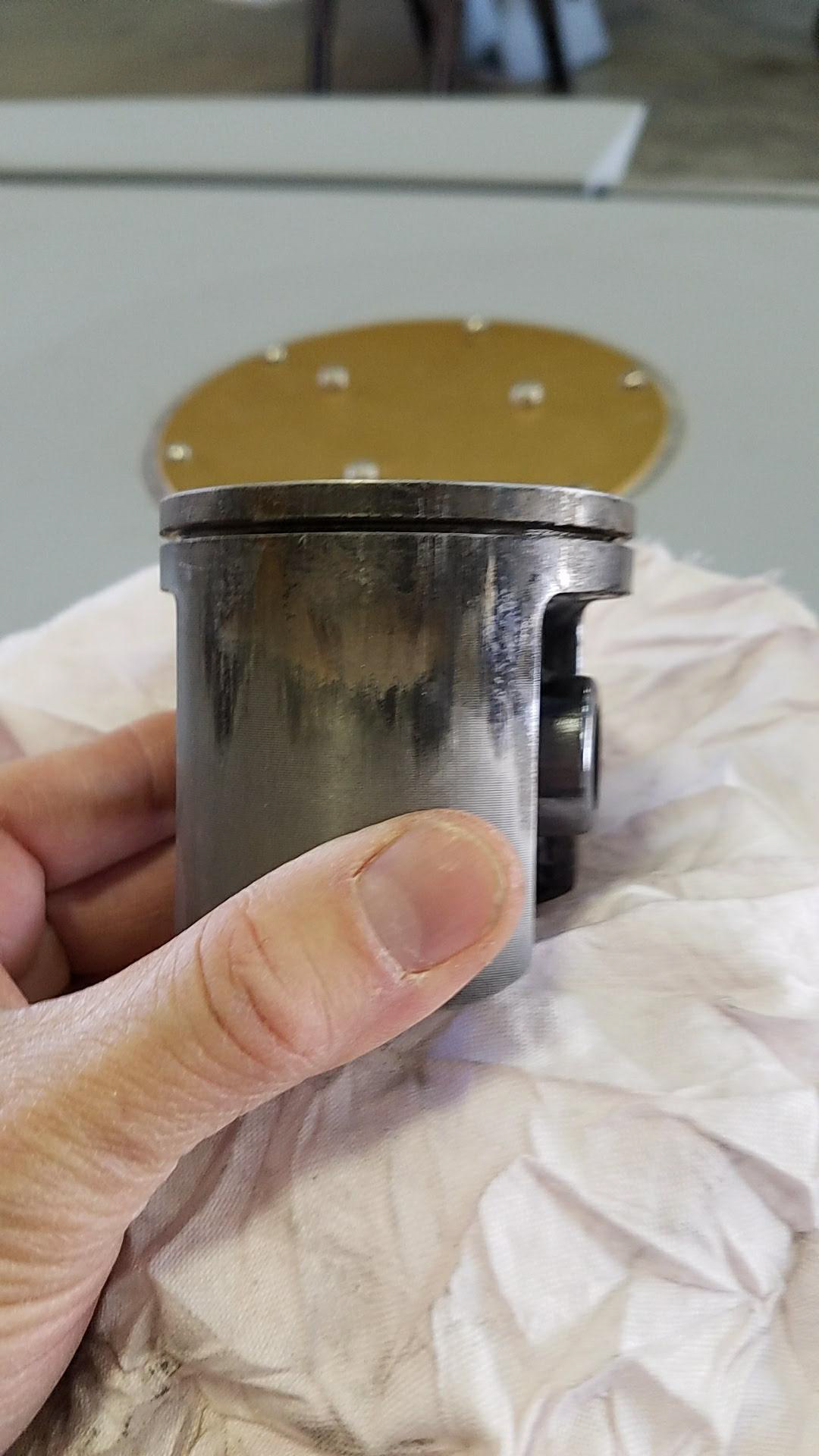
The UAS Technician training consisted of several formal blocks of instruction, culminating in a complete tear-down and rebuild of the aircraft engine. Here, I'm inspecting a piston for wear after removing it from the cylinder head.
We primarily test experimental payloads for several different vendors. This often means troubleshooting and repair of "black box" systems, where we have little or no documentation. Sometimes we have to get very creative to accomplish the mission. Both my electronics and networking skills are put to the test on a regular basis, and I regularly use oscilloscopes, meters, and computer-based troubleshooting techniques.
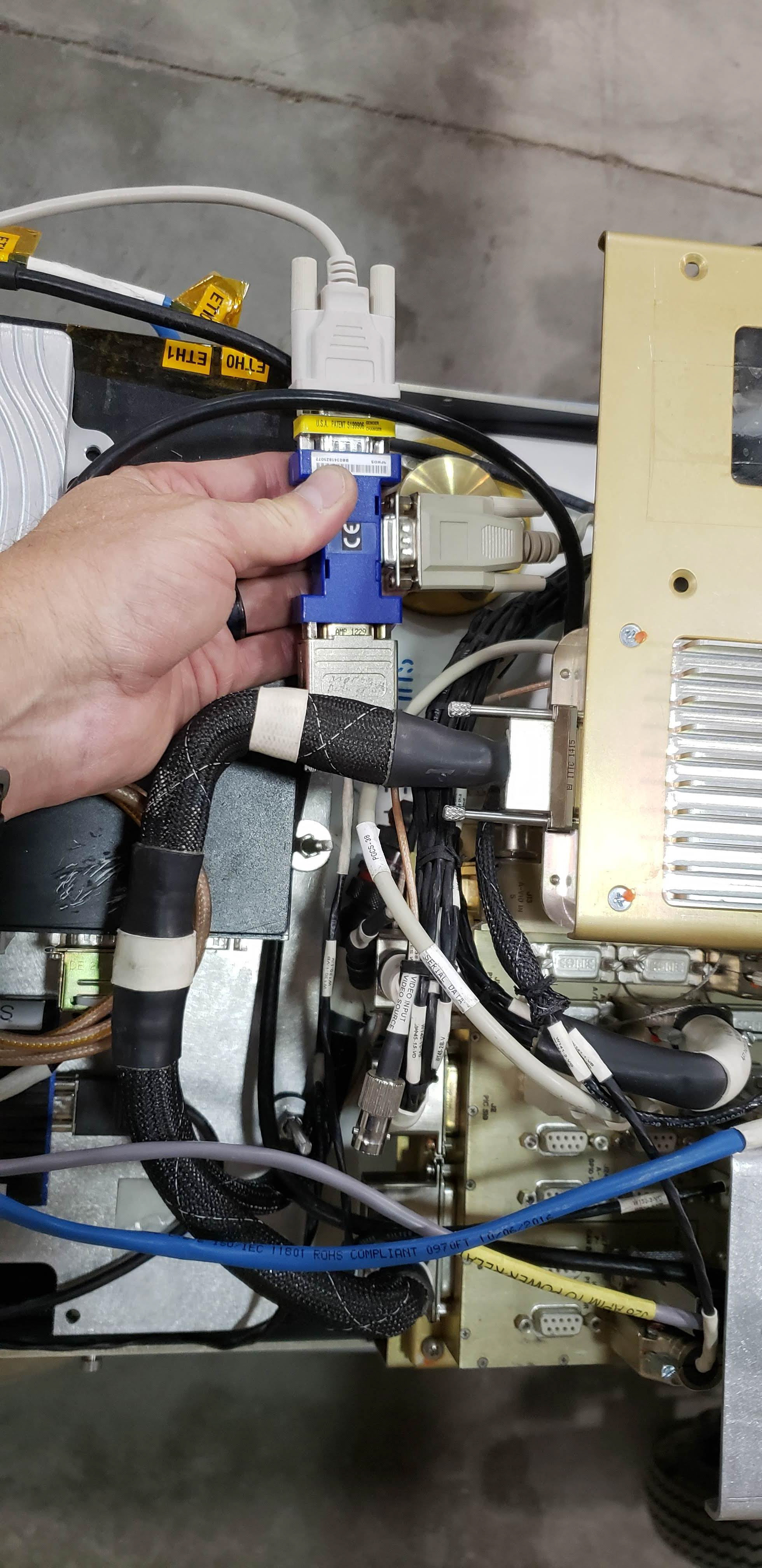
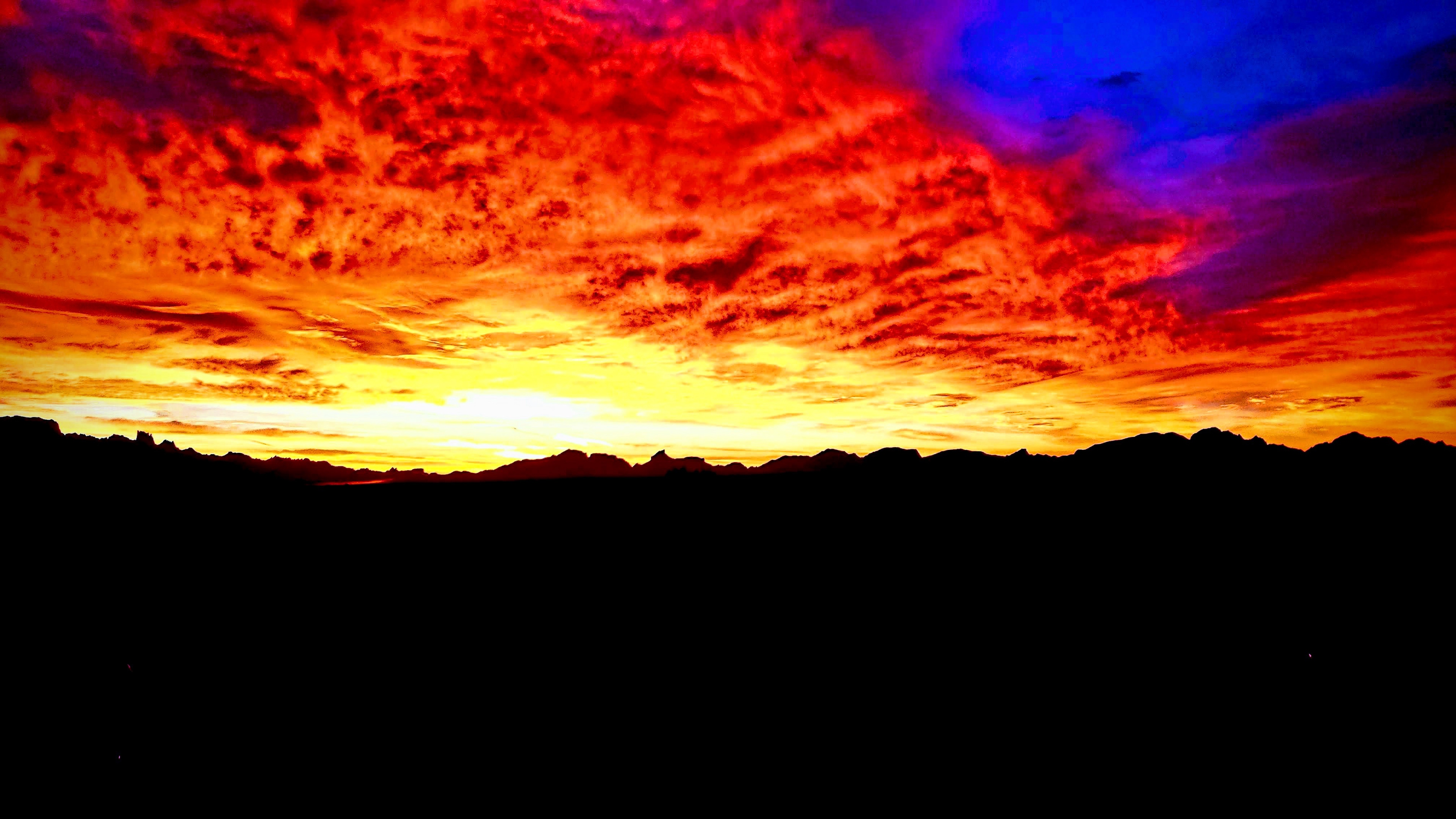
Sunrise, Yuma Proving Ground
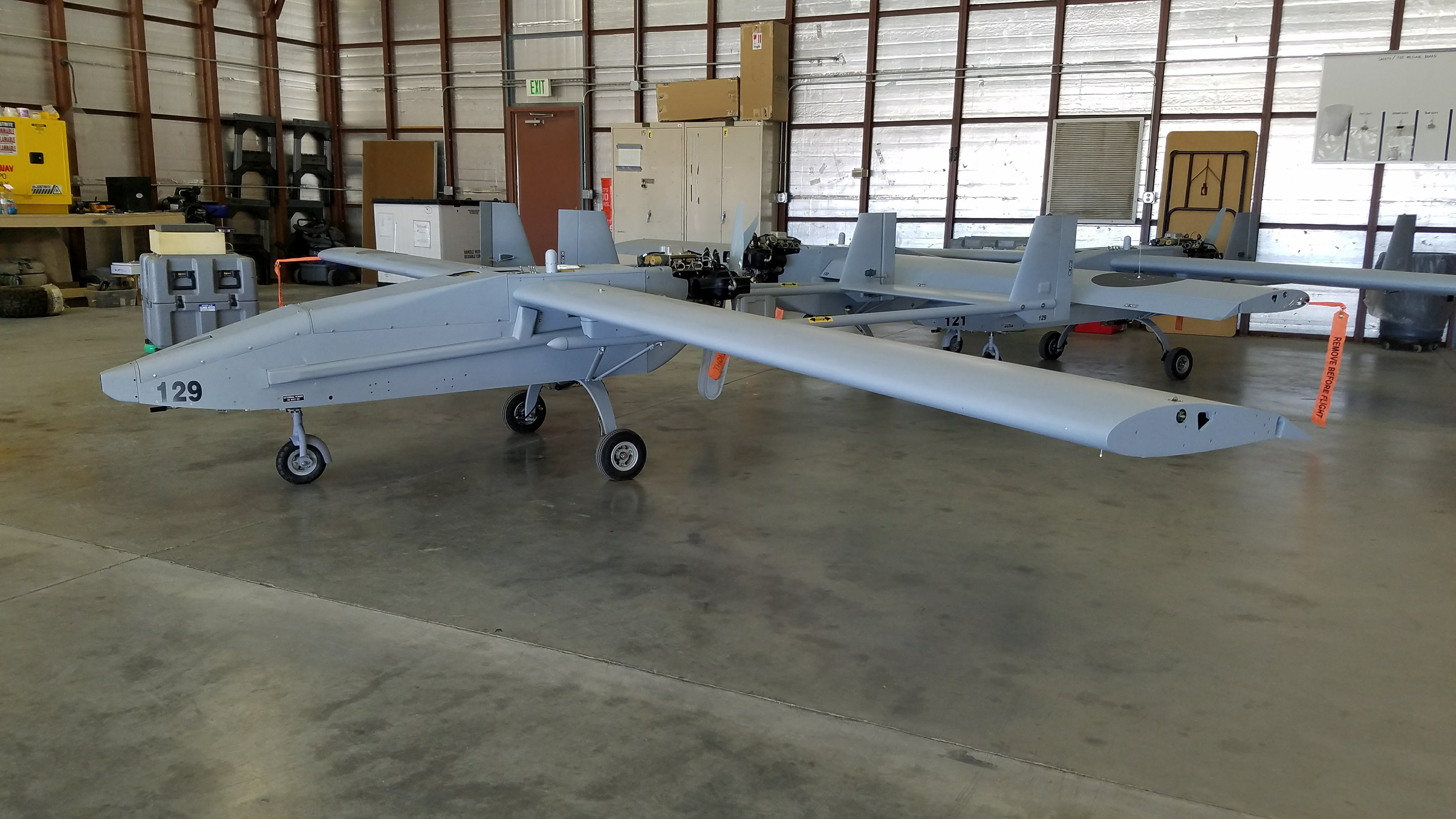
Tigershark 129
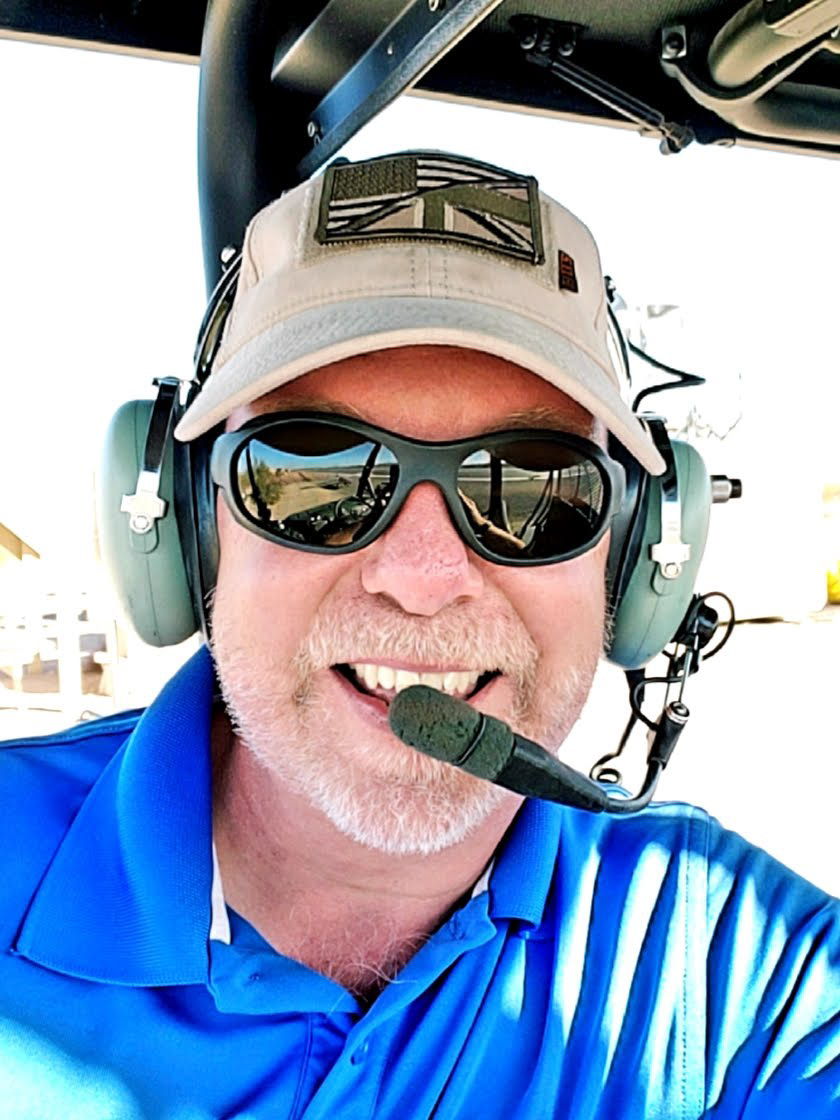
On the flight line
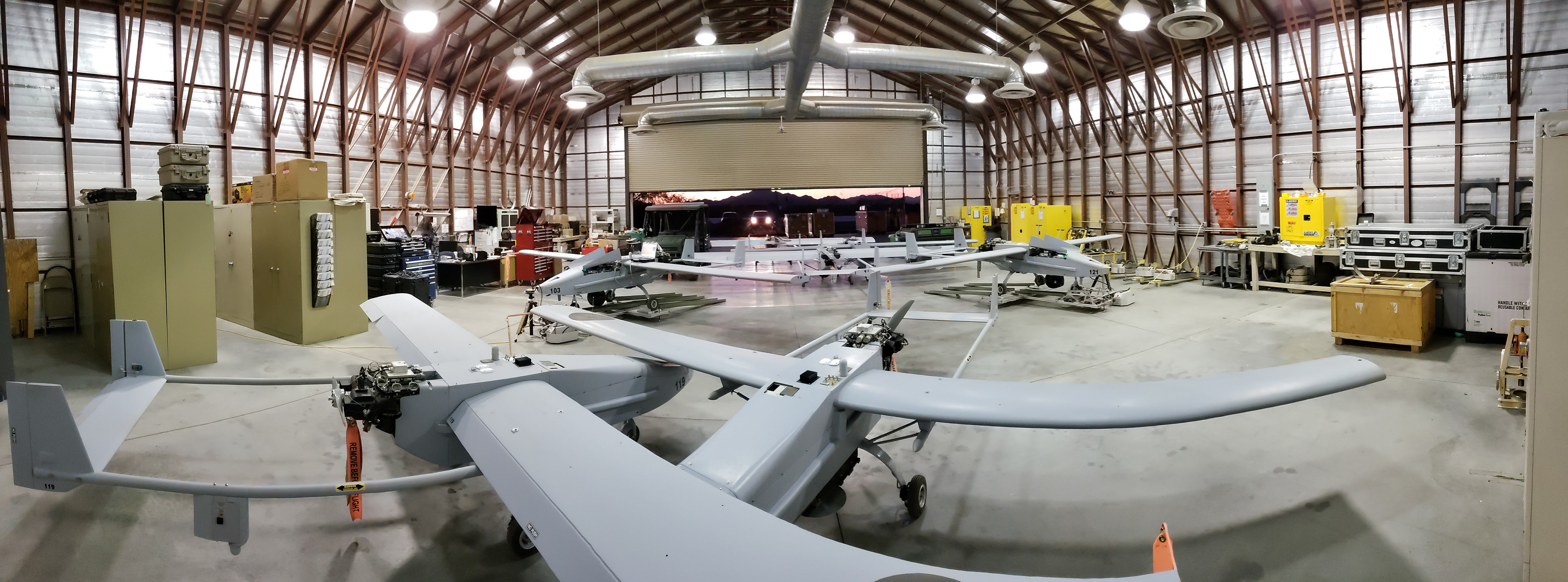
My Hangar
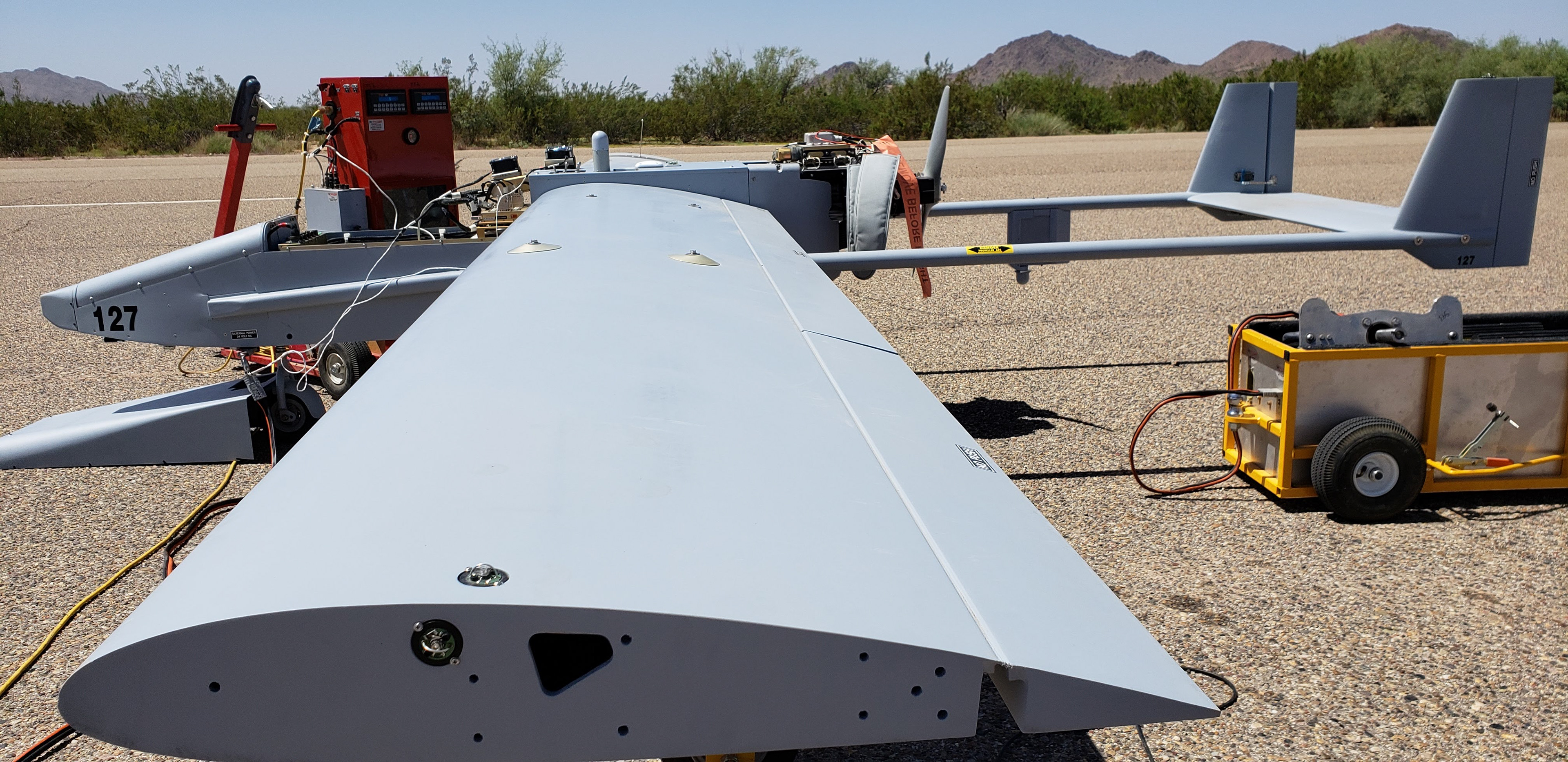
Fuel flow tuning
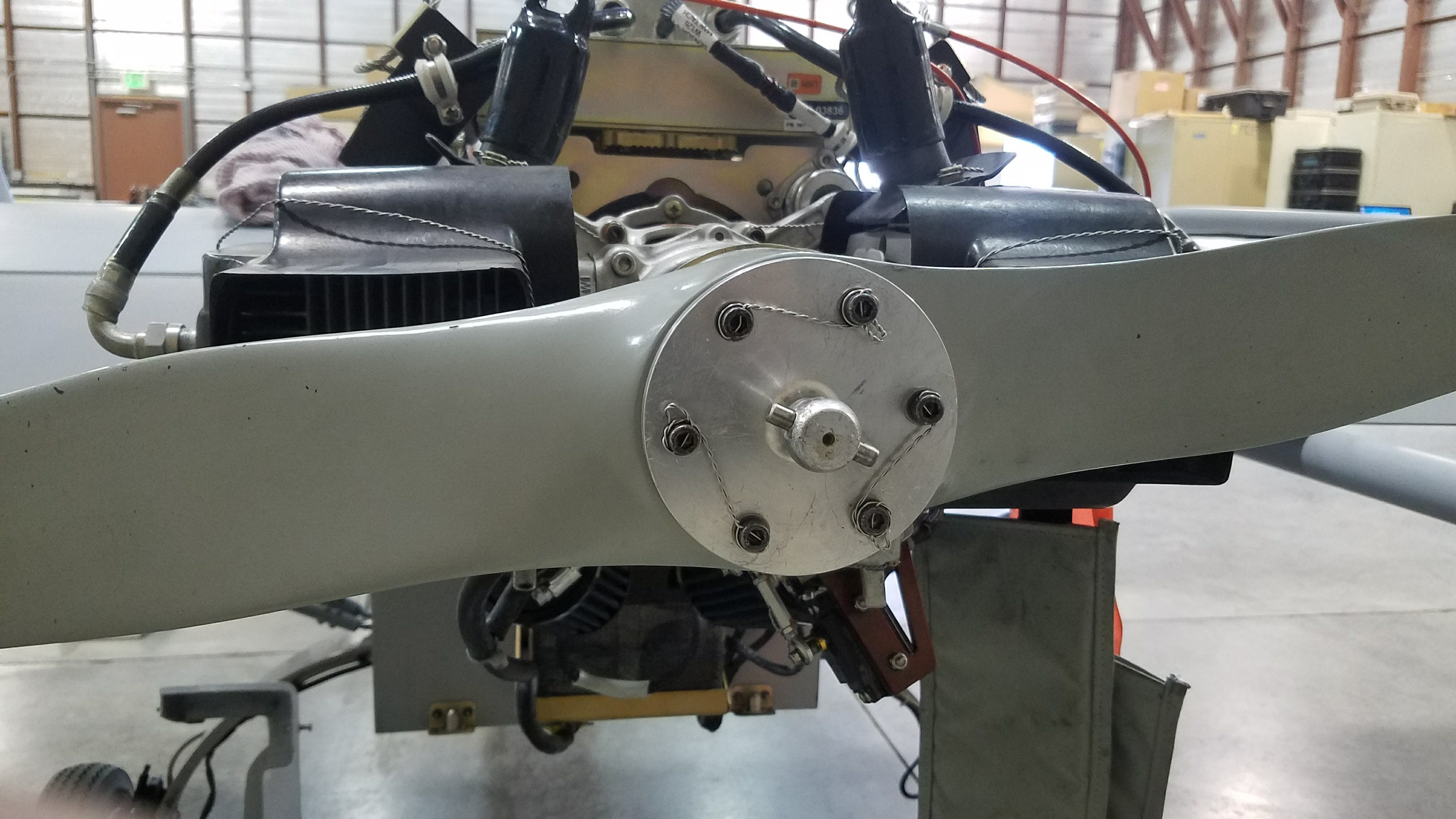